The Process Management Lab, at Boise State University, is helping the Idaho Foodbank improve their internal processes to better serve the community.
The Idaho Foodbank (IFB) was established by the governor in 1984 with warehouses in Boise and Lewiston, adding Pocatello in 1997, to reach every part of the state. In the first 15 years about 4 million pounds of food had been distributed. In the next 10 years, this grew to 67 million pounds. During the pandemic, food distribution jumped another 30%. The IFB distributes free nutritious food through 465 community partners to families in need.
The Process Management Lab (PML) grew out of the organizational consulting experience of Steve Villachica, an Associate Professor in the College of Engineering, and Rob Anson, an Emeritus Professor in the College of Business and Economics. Nearing retirement from the university, they wanted to help non-profit organizations develop more streamlined and sustainable processes to serve their communities, and help the next generation of students and graduates develop these skills. The PML was established in 2020, at the start of the pandemic. It initially focused on improving the core IFB processes, applying its internal methodology in a virtual format. In 2022, the PML is still assisting the IFB, while expanding to work virtually with new non-profit clients.
The Need for Action
Imagine you’re on a mission for a hunger-free Idaho. In 2020, the second-fastest growing state in the country collided with a global pandemic to increase food needs by one third. On the supply side, the Idaho Foodbank (IFB) needed to quickly streamline its processes to manage new COVID-19 challenges–loss of volunteers, sanitation protocols, masks, and social distancing–and accommodate a new expanded warehouse space.
Karen Vauk, IFB President and CEO, noted that IFB needed to invest its resources into process improvement. “We couldn’t afford not to,” she says. “The pandemic presented growth everywhere and need. We needed to become process-based. We needed to make it so that everyone involved had an equal opportunity for success. Frustration was building. We couldn’t go on like we were.”
Even solutions posed new challenges. Jane McLaughlin, the IFB Volunteer Program Coordinator, explained, “In September 2020, IFB moved to a bigger warehouse. We thought things would be better right away, but we quickly learned our previous processes didn’t always work in the new building.”
Collaboration Between the IFB and the PML
The IFB and PML began collaborating in the early days of the pandemic to address redesigning its food-flow processes to meet the state’s food insecurity challenge and retain employees. Thus far, they have undertaken six processes together that comprise the flow of food: planning, procurement, receiving, repacking, distribution, and government reporting.
Overall, these efforts have resulted in various concrete outcomes, such as slashing the spoilage costs of expired foods, and cutting receiving errors by 30% so food can flow more rapidly to the community. Plus, the CEO reported intangible benefits, such as creating new conceptual tools to identify change, the ability to pinpoint issues for quicker response, and improved morale overall.
How Process Improvement Works
To help organizations like IFB, the PML starts working with management to identify the particular goals and challenges they need help with and to list the business processes involved. For each process, the PML will facilitate a pair of workshops over a 2 to 3 week period. The workshop participants form a cross-functional team that comprises hands-on experience with all major steps of that process. Anson notes that “The team members are the essential ingredient! Our facilitation can’t help them design solutions to problems without all of the knowledge about how the system really works. Then afterwards, the success of implementing the changes will require the input and buy-in from everyone.”
The two workshops represent different phases of designing change FROM how work is performed today, TO how it will be performed in the future.
- “As-Is Workshop” first develops extensive maps of the current process steps and decisions. Then, participants use the maps to identify and prioritize pain points or “disconnects” where the process breaks down.
- “To-Be Workshop” focuses on brainstorming new solutions to address the disconnects. Then participants review and prioritize the solutions, to surface those with the greatest potential benefit. The last step is to identify initial implementation plans to start putting solutions in place.
Upon completion, the team has designed new process maps, with specific solutions to existing issues and a plan to implement it. The facilitators describe that plan in a final report for the team and a Powerpoint to present it to leadership.
PML Working Virtually
Prior to COVID, the PML facilitated workshops in clients’ conference rooms, using whiteboards, sticky notes, and sharpies. “But when the pandemic hit”, Anson explains, “we quickly shifted gears to create a virtual method to hold the workshops remotely. The technology had to support rich visual and verbal interactions, and enable us to facilitate participant discussion and entry. Ultimately, we paired Zoom with Mural, a whiteboard program that enabled our facilitators to focus the group’s attention one minute, and open it up to individual participant brainstorming the next.”
Villachica reflected, “While everyone misses working around a table in person, our new technology greatly expands the table. Our face-to-face meetings often had people in remote locations trying to use phone lines to participate in Boise-based workshops. But their participation was unfairly limited because they couldn’t see the whiteboards and had a difficult time hearing. With our new virtual workshops, everyone can participate equally, including those at other sites in Lewiston and Pocatello.”
Example: How PML Facilitated the Repack Process
PML helped the IFB management identify six processes that comprised the flow of food: planning, procurement, receiving, repacking, distribution, and government reporting. Working in-person at the IFB facility, the PML completed its first workshops on receiving product shipments just before the pandemic lockdown.The first process we tackled, on receiving product shipments, and was completed in-person just before the pandemic lockdown.
The PML and IFB worked virtually to address the second process, called “Repack Products,” in Summer 2020. The workshops involved three PML facilitators and eight IFB participants, from three sites separated by hundreds of miles.
Repack involves thousands of volunteer hours each year. Because food (mostly donated) is received from hundreds of sources, and often in bulk, it needs to be repacked into single family servings for distribution. The work process starts with a weekly planning meeting and ends with family food packages on pallets ready for distribution across the state.
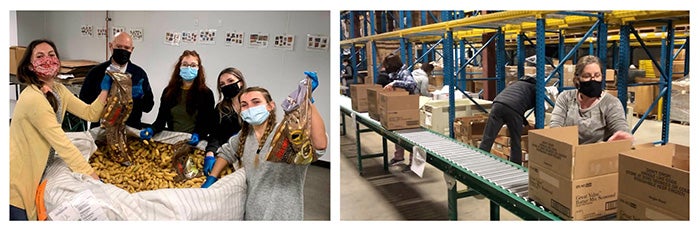
The As-Is workshop involved first training participants to use Mural and identifying success criteria of Repack stakeholders. Then mapping the current process begins with a simple high level map–the 30,000 feet view–shown below in Figure 1. This map shows six phases of work. Each phase of the process must then be expanded into its own detailed map.
Figure 2 depicts an example detailing phase 5: processing a pallet of repackaged goods. A great deal of time and concentration (especially when online) is needed to provide enough but not too much detail, including major scenarios and key decisions.
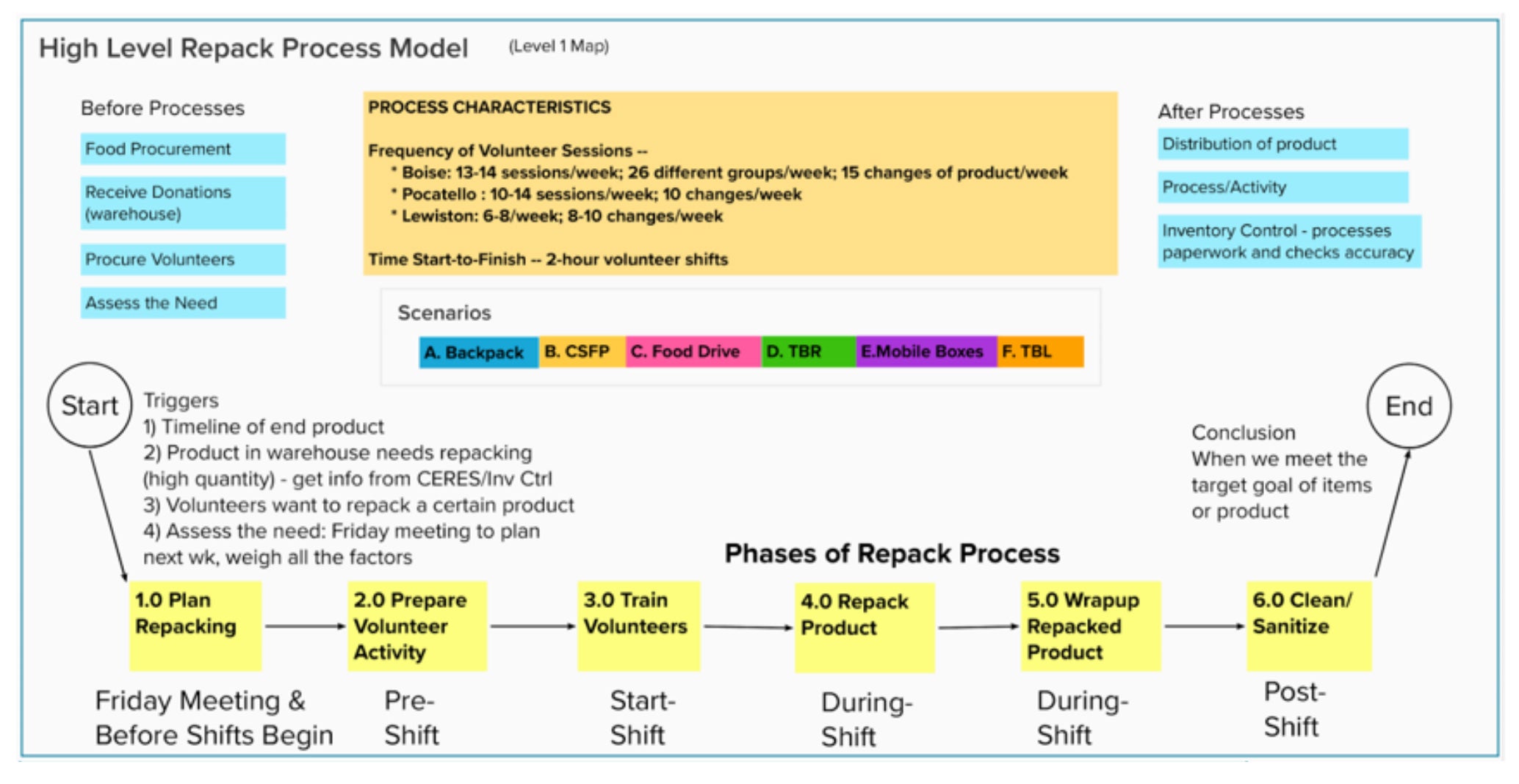
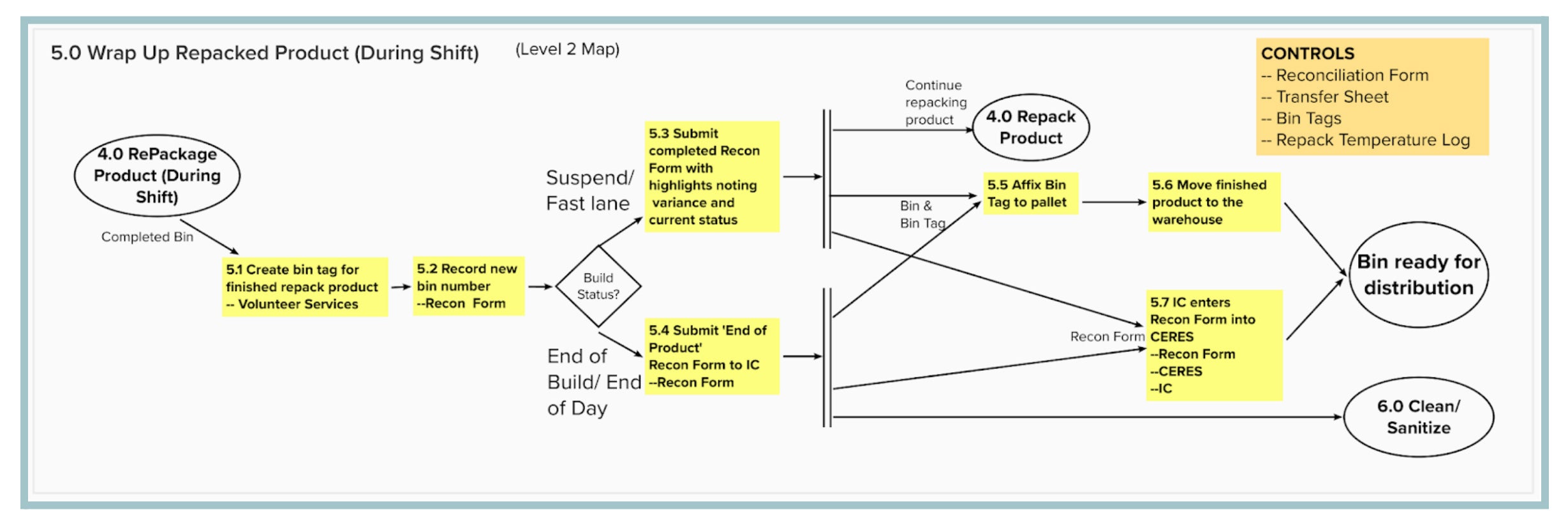
These maps produce multiple payoffs. One is that participants gain a comprehensive understanding of the entire process, where before they may have held but partial view. In the workshop, the maps guide brainstorming problems and solutions; after the workshops, the maps are used for training, continuous improvement efforts, and sometimes system implementation. The maps also help produce buy-in across the process team.
The As-Is workshop concluded with participants brainstorming process disconnects. McLaughlin recounts “those are the frustrating issues we needed to improve. We then reviewed these issues and rated their urgency-to-resolve as low, medium, or high. After the As-Is workshop, PML distributed a report containing all this information for us to check over before we got back together again.”
The subsequent To-Be workshop started by reviewing and revising work from the As-Is. “Then everyone’s keyboards exploded into brainstorming ways to solve the disconnects,” described McLaughlin. “Next, we reviewed and ranked the potential benefit of each solution, and the effort to create them. Finally, we prioritized the solutions with the greatest potential, and identified initial steps to implement them.”
After the workshops, the PML worked with McLaughlin to create a presentation of the top priority changes from the participants to the Leadership Team. The presentation took place a month or so later, and already it showed that four solutions were underway or completed, with three larger ones needing approval for funding or additional resources.
McLaughlin liked the PowerPoint slide deck enough to keep updating it with further projects. It is a standard format for regular check-ins with the IFB’s board of directors and leadership team. “It has provided a framework to give the board ongoing visibility to our work and the challenges we are overcoming,” McLaughlin explained.
Outcomes from the Repack Process Improvement
“I highly recommend using the PML,” says McLaughlin. “These workshops opened all of our eyes, and we prioritized what we needed to do. Some of what we found were small changes that could have a huge impact. For example, looking at the flow holistically, we saw that shifting a part-time person to full-time would help the whole flow. Another small change with a big impact was adding the inventory control supervisor to our Friday morning meetings. We’d never thought of it.” Also, the team set up a white board–another easy, low-cost, and big-impact solution–to keep communication flowing (see Figure 2).
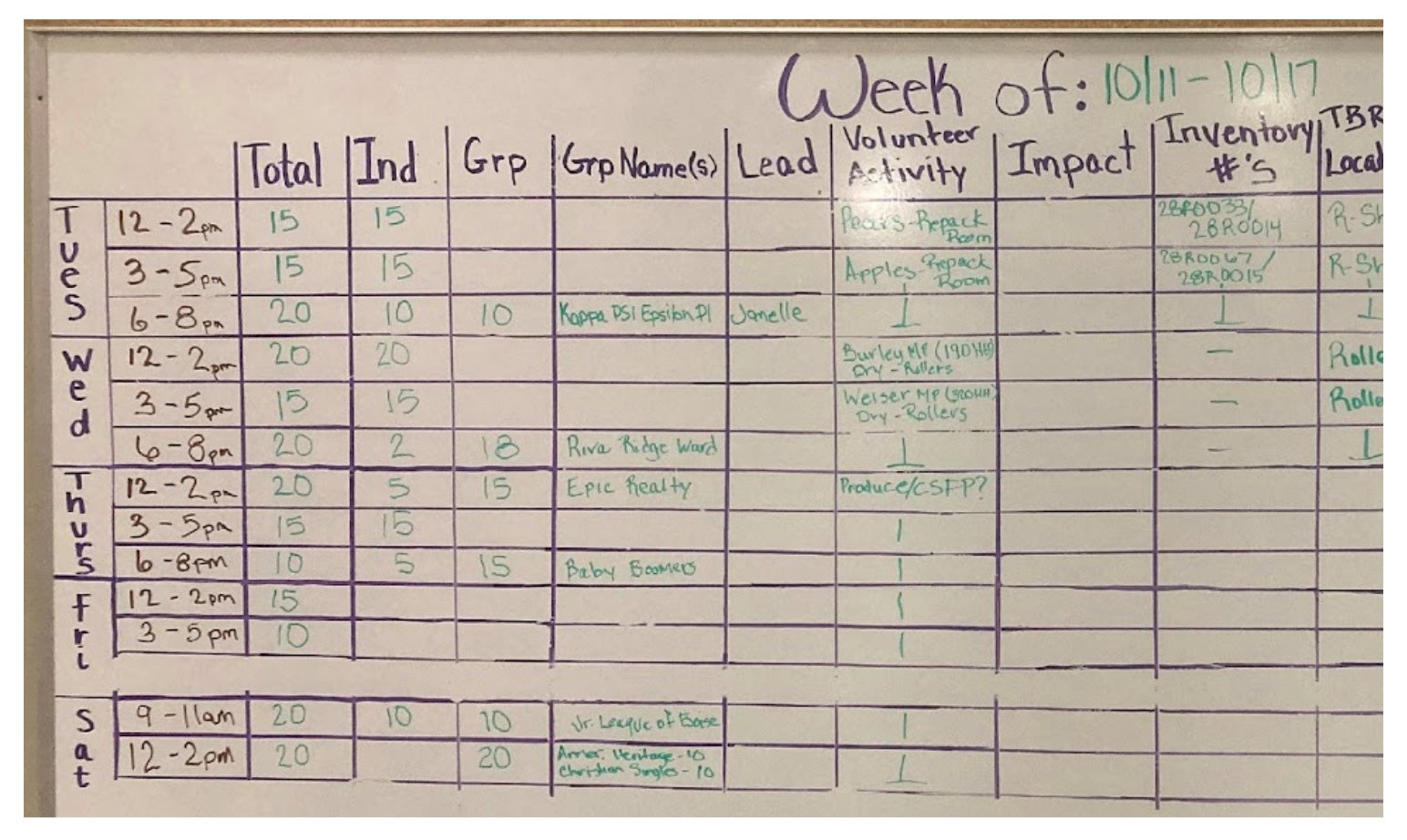
Additionally, the Repack team identified some larger solutions that required approval for resources. Two involved training staff members, running a forklift and querying information from the inventory system, which could remove bottlenecks that occurred in evenings and weekends when volunteers were available but warehouse and inventory staff were not.
IFB Outcomes from the Improving a Set of Processes
Over two years, the list of business processes improved by PML at the Idaho Foodbank has grown to six, with another about to start and others being considered. This is a considerable investment of staff time and energy, especially when adding in the time to implement the solutions. As a result, it is important to pay close attention to staff capacity to maintain a productive balance among current operations, new solutions, and future process improvement workshops.
In a recent presentation, Randy Ford, IFB Chief Operations Officer, identified some of the tangible benefits recognized from the process improvement efforts:
- Reduction in spoilage cost of expired foods reduced from $93K to $250/month over the last 4 months.
- Receiving errors were cut by 30%. Plus, there is a multiplier benefit as removing errors at the beginning helps the rest of the food flow process.
CEO Vauk has highlighted some of the intangible benefits. She had sensed growing frustration before these efforts started. In addition, faulty processes have created barriers to successfully making changes. But engaging staff in process improvement workshops and the subsequent status meetings with IFB leadership helped create a new climate for success. “Just to have the documentation was so significant! Plus, we have conceptual tools to understand the process and common language to facilitate better outcomes. Now we can pinpoint issues and respond much faster. There is also much better morale, which is better for everyone.”
Villachica notes, “We’re so proud that our long IFB partnership has helped them build capacity to meet their mission and serve our Idaho neighbors. We’re also proud that the graduate students and graduates who are our Lab Associates have gone on to find their dream jobs in the field and contribute to our website. We’re just lucky to work with great clients and Lab Associates. Everybody wins.”
About the Process Management Lab
The PML was founded in the Spring of 2020 in the Department of Organizational Performance and Workplace Learning (OPWL), College of Engineering, at Boise State University.
Our Mission is to provide affordable process planning, redesign, and implementation services to the non-profit community while developing facilitation and consulting skills in the next generation of professionals.
The principles bring extensive consulting experience to the PML. They include Dr. Steve Villachica and Dr. Rob Anson, from the colleges of Engineering and Business & Economics respectively, who founded the lab. They were joined by Dr. Tony Marker from OPWL, and Fran Caprai who has been managing Information Systems efforts in the private sector for years.
Current master’s students and graduates of the OPWL program work as Lab Associates. They help facilitate the workshops and create learning objects that appear on the PML website. They bring a variety of important skills, experiences, and new ideas.
Contact Information
Dr. Steve Villachica Email: stevevillachica@boisestate.edu Cell: (970) 371-4627
Dr. Rob Anson Email: ranson@boisestate.edu Cell: (208) 869-2801
About the OPWL Program
The Organizational Performance and Workplace Learning (OPWL) program helps prepare students for careers in the areas of instructional design, training and development, e-learning, workplace performance improvement, organizational development, program evaluation and performance consulting.