Nuclear power plants account for 20% of the country’s electricity production and have helped cut down on the reliance of fossil fuels. At the heart, or core, of a nuclear reactor are the fuel rods, which is where nuclear fission occurs. Most fuel rods, however, are only in a reactor for a total of six years, with a third being replaced every two years, resulting in a continuously growing stockpile of used nuclear fuel.
Used fuel rods are typically placed in deep pools of water for 10 to 20 years before they have cooled enough to be safely dried and transported to long term storage. Due to limited pool capacity in the US, as well as the continuous delays in building a long-term repository, there is a growing need to safely store the nation’s nuclear waste.
Hoping to tackle this problem, assistant professor Brian Jaques of the Advanced Materials Laboratory, and materials science and engineering doctoral students Kaelee Novich and Samuel Pederson collaborated with assistant professor R.A. Borrelli and Richard Christensen of the Nuclear Engineering Department at the University of Idaho, and a Japanese vacuum casting company, Sakae Casting Co.
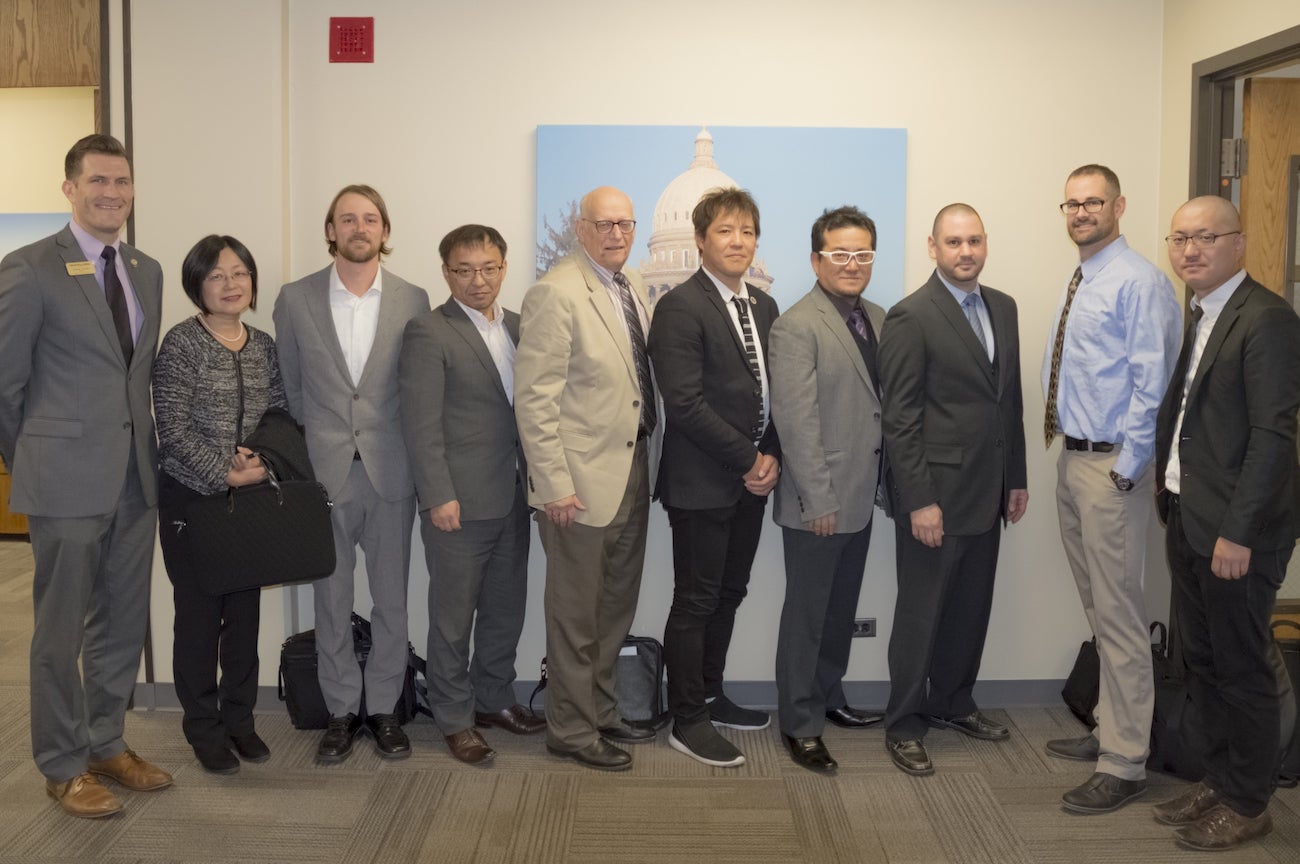
“Collaborating with Sakae and the U of I for this project was such a good experience. Research in the private sector can be different from research in academia or at government facilities, so when all three work together, good innovation happens,” said lead author on the study, Novich, a Top Ten Scholar and awardee of the 2020 Innovations in Nuclear Technology Research and Development Award.
With the support of a nearly $240,000 Idaho Global Entrepreneurial Mission (IGEM) grant, the innovative team of collaborators worked to advance dry-cask nuclear storage methods, which could foreseeably remove the need for extended traditional pool storage of spent fuel rods.
“The ability to innovate in the way in which we currently store used nuclear fuel is paramount to the expansion and use of nuclear energy in our country. The technology that was developed through our collaboration with the University of Idaho and Sakae Casting combines materials science and heat transfer with nuclear physics and processing prowess. The solution to inherently safe, long term and robust fuel storage is at our finger-tips,” said Jaques.
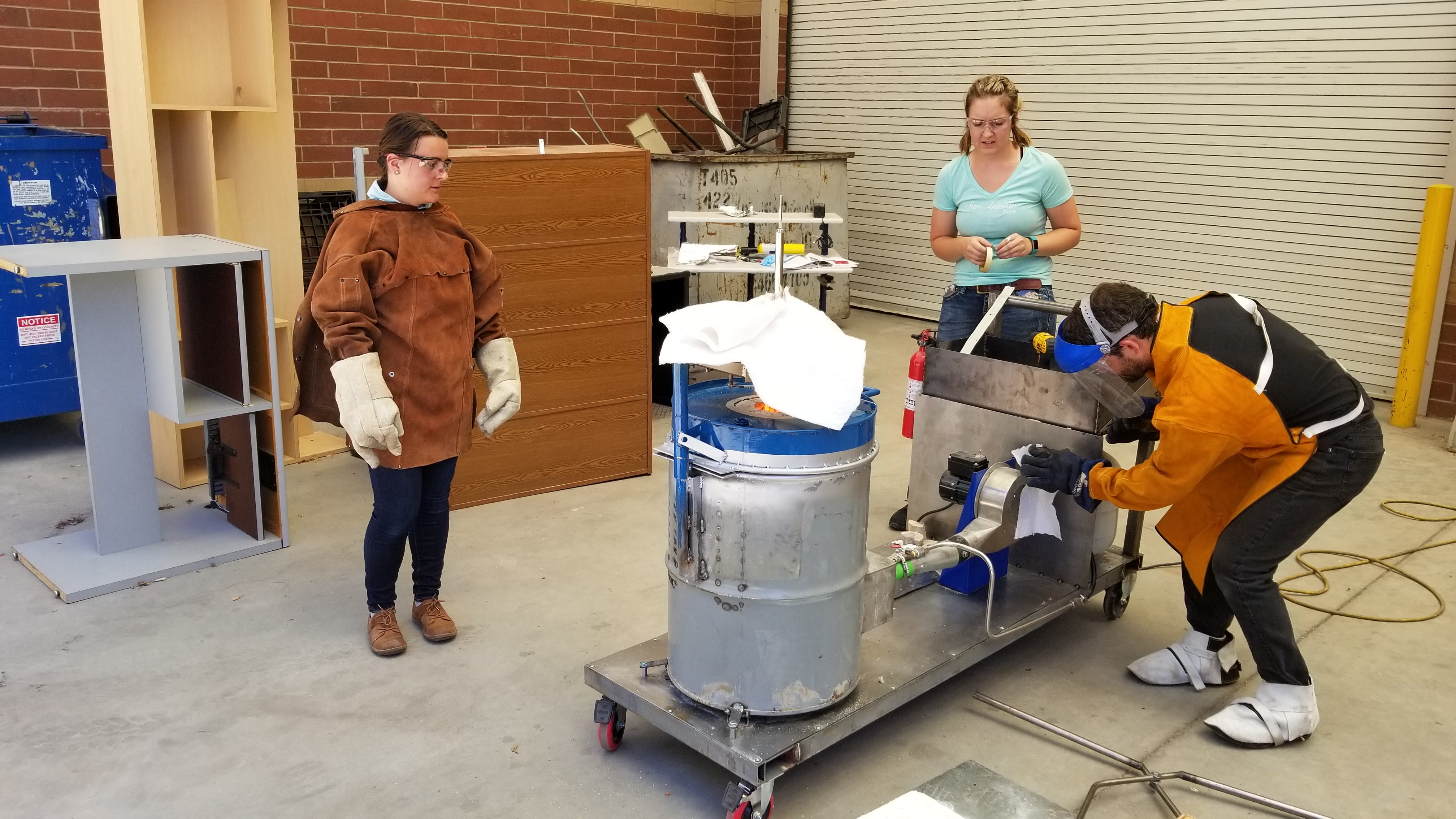
Dry cask storage methods involve ‘cooled rods’ (or rods that have been contained in a pool for several years) to be stored in steel casks, surrounded by inert gas and stored. The team’s innovation is working to remove the need for pool containment at all, thereby minimizing the risks associated with pool containment, criticality concerns, and not drawing upon a storage system with a finite capacity.
The collaborators have been researching the effectiveness of using vacuum sand casting to create dense aluminum plates mixed with boron carbide particles (to shield the neutron radiation), and an embedded water-filled serpentine coil to convectively (and passively) cool the cask contents. This low-cost method of dry cask storage offers a commercially viable alternative to traditional containment in pools of water.
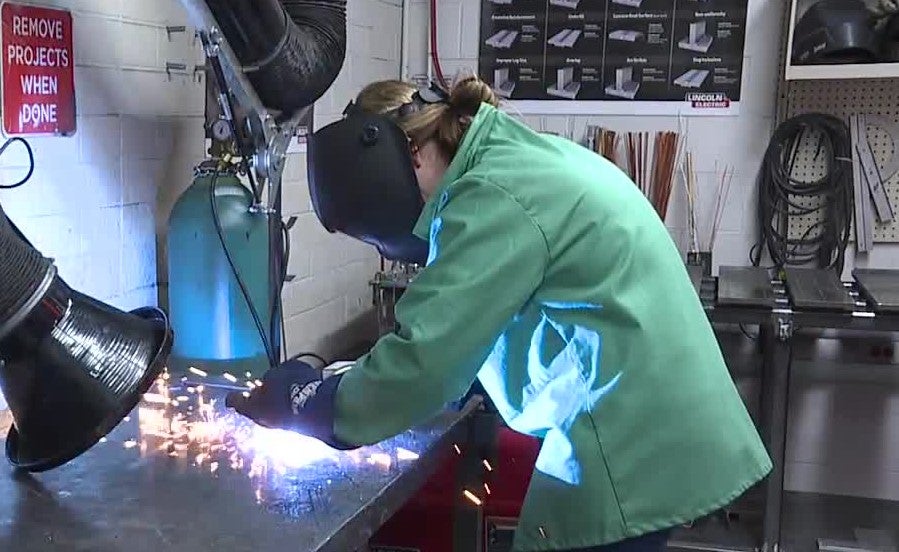
“The cask panels were created using many of the resources available in Boise State’s Engineering Innovation Studio which provided me the opportunity to get trained on most of the equipment in the studio,” said Novich. “We used a furnace to melt aluminum down and would mix boron carbide into the aluminum while in the furnace before pouring it into a sand mold. This process is similar to adding ingredients when making a dough for cookies or bread.”
Boise State, with the help of Sakae Casting, focused primarily on optimizing the homogeneous dispersion of boron carbide particles during the sand casting of aluminum. Concurrently, the University of Idaho performed heat transfer calculations and simulated neutron flux due to the decay of used fuels that helped decide the necessary wall thickness and geometry of the cask designs, which was coupled with boron carbide concentration.
The team’s article, titled “Synthesis of boron carbide reinforced aluminum castings through mechanical stir casting,” was published in the Journal of Composite Materials, and can be read at https://doi.org/10.1177/0021998320987597.
-By Kalee Novich, Sam Pedersen, Brian Jaques and Brianne Phillips