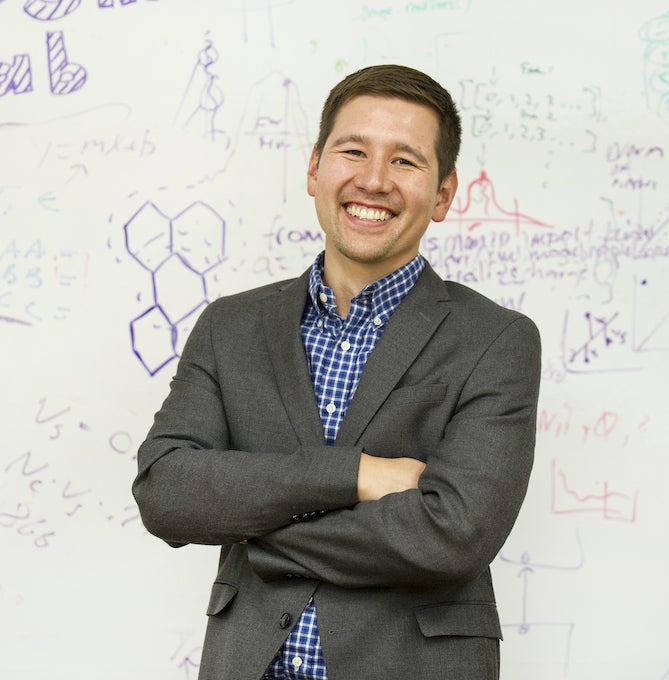
When one is lucky enough to get the window seat, the view of an airplane’s wing peppered with metal rivets is a familiar one. But through a collaboration with the University of South Carolina and the University of Southern Mississippi and the support of a $5.7 million dollar NASA University Leadership Initiative (ULI) grant, Boise State research will be integral to shaping airframes of the future, made of a completely different material: thermoplastics.
Thermoplastics are materials made from polymers that get softer when heated, explained Boise State research lead Eric Jankowski, an assistant professor of materials science and engineering. Recognizable items already made from thermoplastics include snowboards and skis.
Today, high-selling aircraft like the Boeing MAX and the Airbus A321 can be produced at a rate of two to three aircraft a day. Michel van Tooren, the initiator of the NASA proposal and the former director of University of South Carolina’s SmartState Center for Multifunctional Materials and Structures, predicts that urban air transport will ultimately require 100 aircraft to be produced a day, hence the pressing need for alternative manufacturing methods and materials.
“How do you do that?” van Tooren rhetorically asked. “And if you do 100 aircraft a day and it’s maybe 30 blades on an aircraft, then that’s 3,000 blades a day. There’s no technology available at the moment that creates such an enormous number of aircraft-quality products, and that’s the big challenge.”
That’s where thermoplastics offer an opportunity to revolutionize the airframe industry.
“Thermoplastics are good for airframes because we can ‘weld’ together small pieces into larger structures without using nuts and bolts,” said Jankowski. “Making airframes without nuts and bolts makes them stronger because parts usually break where they’re fastened together with nuts and bolts. The welding of thermoplastics is different than with metal, but is used to essentially melt the surfaces of two pieces, which then join together, kind of like nano-scale velcro.”
Unlike traditional metal airplane wings, which must be put into giant ‘ovens’ to be welded together, thermoplastics can be mass-manufactured and assembled in small sections. However, prior to making airframes completely out of thermoplastics, it is essential that researchers know exactly how certain polymers will react to a given set of conditions.
“The properties of a thermoplastic, like its density, how easily it bends, depend on how its ingredients are arranged. We use computer simulations to predict how the ingredients of thermoplastic polymers arrange so we can better pick the ingredients and manufacturing conditions that will give us the materials that are the best for rapid manufacturing of polymer-based parts for aircraft,” said Jankowski.
In tandem with the University of Southern Mississippi, Jankowski will model the rearrangement of polymers using supercomputers to develop better thermoplastic tapes for joining wing airframe components. The University of South Carolina then will take these advancements to weld airframes without the use of any traditional fasteners. Jankowski believes the interdisciplinary venture will enable heretofore unthinkable innovation.
“I’m so excited for the collaboration of our team. It’s a real opportunity and privilege to have expertise at such disparate length scales working on this project. The University of South Carolina’s team are world leaders in manufacturing. The University of Southern Mississippi are world leaders in polymer processing and chemistry,” said Jankowski.
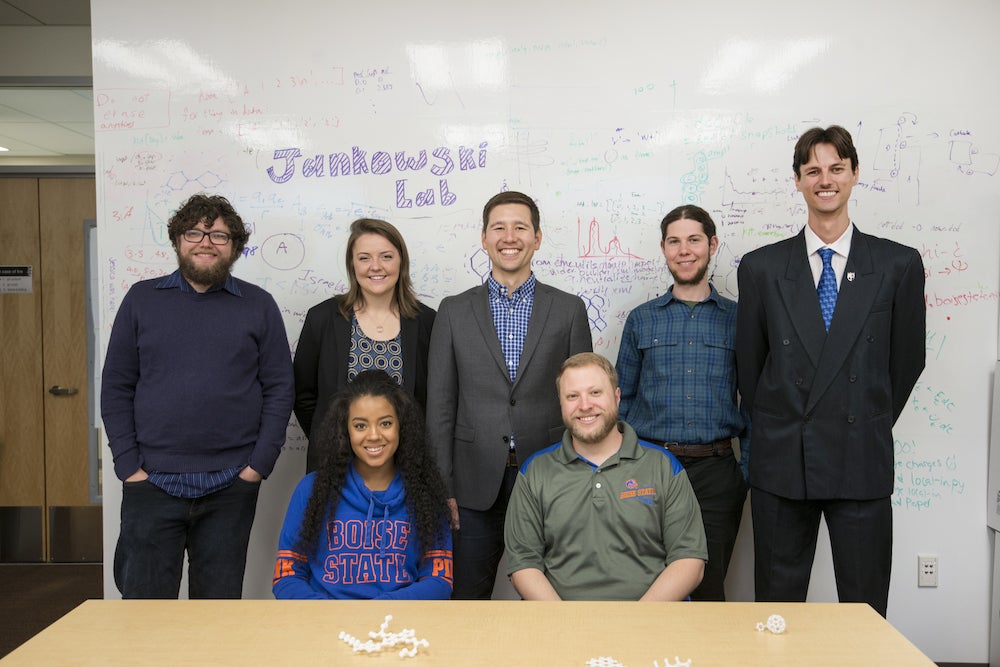
Jankowski will be conducting this research with current student Chris Jones, a first-year materials science and engineering graduate student, and newly-hired postdoc Rainier Barrett who received his doctorate in chemical engineering from University of Rochester.
“At Boise State, we bring expertise in modeling that’s tailored to understanding these polymers, so we can help optimize how the formulations and tapes are made. It’s a real opportunity to design airframes from the atoms, all the way up,” he said.
Jankowski credits former students alumna Mone’t Alberts (BS, materials science and engineering, ‘20), now a doctoral student at Boise State; Mike Henry, a fifth-year materials science and engineering doctoral student; and alumnus Stephen Thomas (PhD, materials science and engineering, ’18) as being instrumental to the work leading up to this grant.
The University Leadership Initiative was created by the NASA Aeronautics Research Mission Directorate (ARMD). This $32.8 million ULI has five team leads, including South Carolina, North Carolina Agricultural and Technical State University, Oklahoma State University, Stanford University and the University of Delaware. The ULI will allow these universities to build their own teams and formulate their own research paths in hopes that their findings support the NASA ARMD portfolio and the larger U.S. aviation community.
– By Brianne Phillips