Research Details
Magnetostrictive Materials
Magnetostrictive materials exhibit mechanical deformation when driven by a magnetic field or vice versa. These unique properties make them highly versatile, with applications ranging from actuation and sensing to energy harvesting. While the magnetostrictive effect is inherent to all ferromagnetic materials, only specific alloys—such as those combining iron with rare earth elements, gallium, or aluminum, as well as certain amorphous metals—offer sufficiently high levels of magnetostriction to be commercially viable. Magnetostrictive materials are suitable for harsh environments (i.e., high temperature, radiation) and biomedical applications.
Ultrasonic waveguide thermometer (Active)
Sponsor: DOE Advanced Sensors & Instrumentation (ASI) Program; DOE Consolidated Innovative Nuclear Research (CINR) program
Ultrasonic thermometry has the potential to improve upon temperature sensors currently used for in-core temperature measurements. Ultrasonic thermometers (UTs) work on the principle that the speed at which sound travels through a material (acoustic velocity) is dependent on the temperature of the material. Temperature may be derived by introducing a short acoustic pulse to the sensor and measuring the time delay of acoustic reflections generated at acoustic discontinuities along the length of the sensor. UT temperature measurements may be made near the melting point of the sensor material, allowing monitoring of temperatures potentially in excess of 3000 °C.
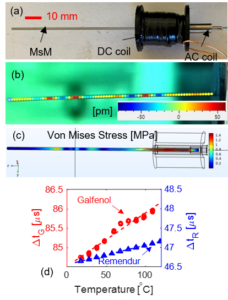
The figure above shows a typical UT design based on iron-gallium alloys or Galfenol. We have developed an accurate and efficient multiphysics model that is able to capture the acoustic wave propagation in the waveguide.
Additive manufacturing of magnetostrictive materials (Active)
Sponsor: NASA Established Program to Stimulate Competitive Research (EPSCoR)
Previous Sponsors: NASA Idaho Space Grant Consortium (ISGC) grant
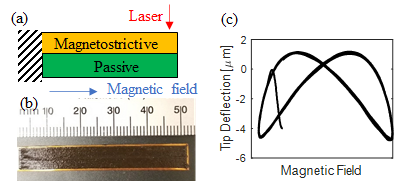
Our group has successfully printed magnetically-active composites by dispersing magnetostrictive particles in polymeric matrices. By printing magnetostrictive composites on top of passive substrates, we further developed cantilever actuators, also known as unimorph actuators, as shown in the figure on the left. When a magnetic field is applied along the longitudinal direction of the beam, the magnetostrictive layer deforms while the passive substrate tends to maintain flat. Therefore, the unimorph actuator outputs micro-scale and butterfly-shape tip deflection. This actuator can be potentially used for precision drug delivery or optical instrument control.
Piezoelectric Materials
All-printed tactile sensor (Active)
Sponsor: NASA EPSCoR
Previous Sponsor: SEMI FlexTech
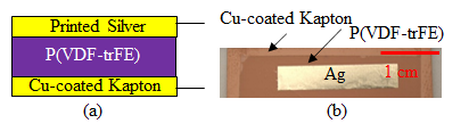
A typical piezoelectric tactile sensor consists of a piezoelectric layer (e.g., PVDF-trFE) sandwiched by a pair of electrodes, as shown in the figure on the left. Our group has printed the PVDF-trFE layer and top silver electrode. In collaboration with Dr. Benjamin Johnson (Boise State), our group has developed signal processing and wireless data transmission circuits for piezoelectric sensors for the purpose of measuring carotid pulses.
Printed surface acoustic wave (SAW) sensors
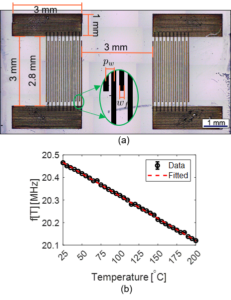
Shape Memory Materials
Shape memory materials exhibit coupling between thermal and mechanical energies. Specifically, our group focuses on shape memory polymers that can return from a deformed shape (temporary shape) to the memorized shape (permanent shape) when they are heat up beyond the transformation temperature. This unique property has enabled innovations in morphing structures, actuators, and self-healing structures.
Morphing Electronics (Active)
Sponsor: NASA EPSCoR
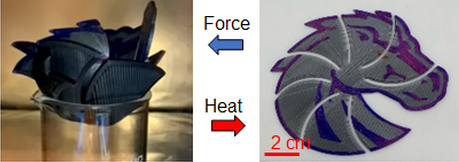
Our group has printed shape memory polymer structures that exhibit more than 60% deformation at a transformation temperature of around 70 °C. The figure on the left shows a printed morphing structure transforming between 2D Bronco logo and 3D rose shape. The video below shows a morphing electrical circuit printed on top of shape memory polymers.
Multiphysics Modeling
Multiphysics Modeling of Surface Acoustic Wave Transducers
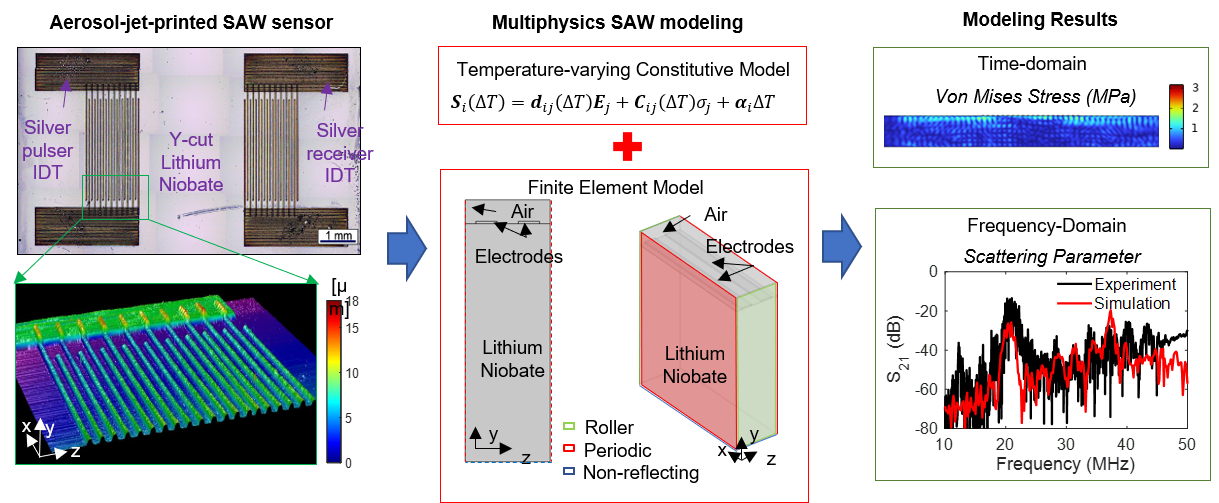
Constitutive model for Terfenol-D Composites
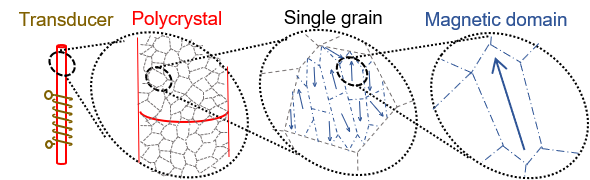
In collaboration with National Cheng Kung University, we developed a mathematical framework for two-phase magnetostrictive composites composed of oriented or non-oriented magnetostrictive Terfenol-D particles embedded in passive polymer matrices. The phase constitutive behavior of the monolithic Terfenol-D with arbitrary crystal orientations is represented by a recently developed discrete energy averaged model. This unique Terfenol-D constitutive model results in close-form and linear algebraic equations accurately describing the nonlinear magnetostriction and magnetization in magnetostrictive composites subjected to a given loading or magnetic field increment. The effectiveness of this new mathematical framework in capturing magnetostrictive particle size orientation, phase volume fractions, mechanical loading conditions, and magnetic field excitations are validated using a series of experimental data available in literature. Compared to existing models that prevalently addressed particle orientation in composite constitutive level, the model framework in this study directly handles particle orientation in the phase constitutive level, and therefore achieves enhanced efficiency while maintaining comparable accuracy.
Finite element model for LVDT
Sponsor: DOE Advanced Sensors & Instrumentation (ASI) Program
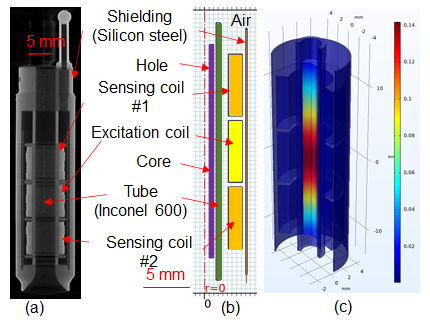
Linear Variable Differential Transformers (LVDT) sensors, known for superior in-pile performance under irradiation, are available to provide micron-scale resolution data enabling the evaluation of fuel performance. Such a high resolution measurement requires a careful understanding of not only sensor itself, but also the complete implementation strategy, including thermal conditions, hardware selection and design, and data processing. To evaluate sensor performance, reduce sensor size, and optimize sensor configurations, this study first develops a finite element model in COMSOL Multiphysics for commercial LVDT sensors in order to investigate the impact of each component’s dimensions and material properties. This study then establish a finite element model including a through hole at the LVDT core to allow for instrumentation pass-through, such as a fiber optic cable.
Sponsors and Collaborators
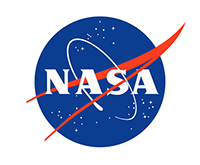
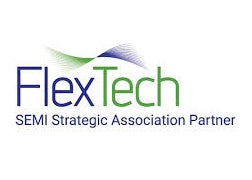
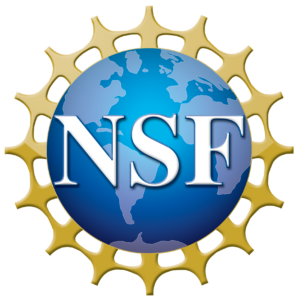
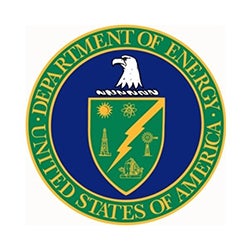