Not Snug Enough for You?
This device keeps you tight all day long!
One of the most common issues that lower leg amputees have is finding the perfect fit for their prosthetic leg. Due to the amputee’s activity and diet, the volume of an amputee’s residual limb fluctuates throughout the day that distorts the fit of their prosthetic socket which leads to discomfort, pain, and sometimes even serious medical complications. A new prosthetic socket design is required which has the capabilities of sensing a change in the user’s volume around the residual limb and actively provides action to fix the situation. Using new software, our team derived a solution to allow for a socket to accommodate for this fluctuation.
The Team
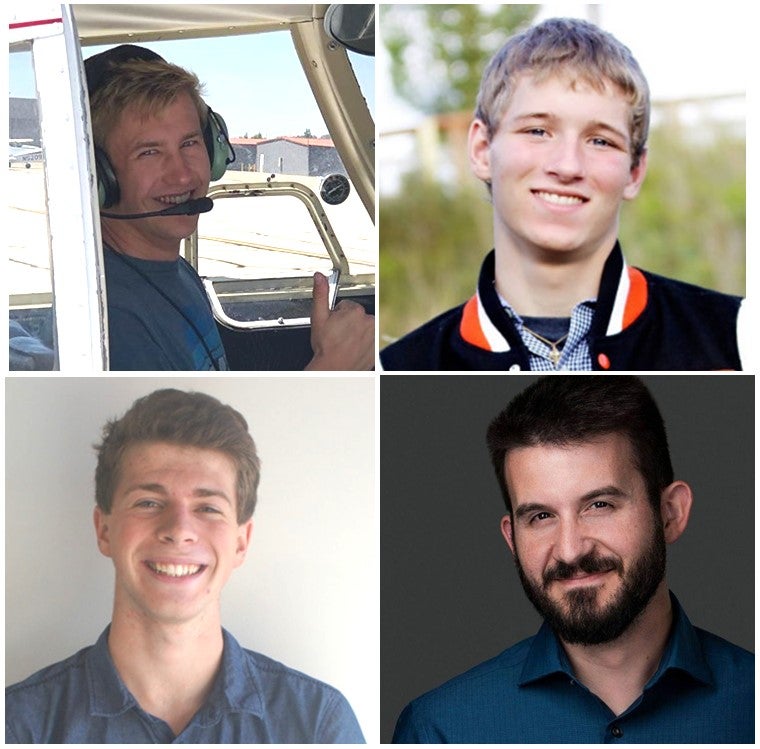
Members
- Garrett Auby
- Preston Bellville
- Matthew Walsh
- Aaron Weeks
Capstone Design Coordinator
Prosthetic Socket Improvements
Smart Amputee Socket Project
Problem Statement
Amputees typically see volume fluctuations in their residual limb throughout the day that affect the fit of their prosthetic socket. This can lead to discomfort, pain, or even serious medical complications. A new design is required which has the capabilities of sensing a change in the user’s volume around the residual limb and actively providing action to fix the situation.
Benchmarking
Flexible Silicon Socket
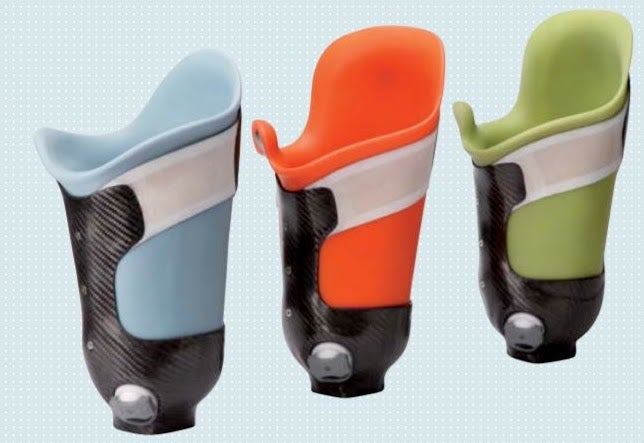
These sockets are made of flexible silicon that are fitted to each patient.
Pros
-
Easy to clean silicone lining
-
Simple to use
-
Lightweight
Cons
-
Not adjustable
-
The user must manually don extra socks throughout the day to manage the tightness of the prosthetic
Link: https://www.ottobock.com/en-au/category/32334
Vacuum Seal Liners
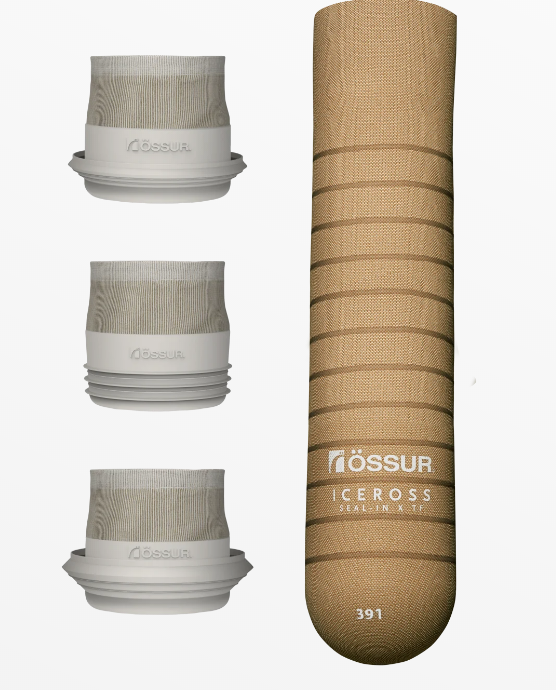
This seal fits over a liner that the amputee wears. This seal is able to flex and keeps pressure between the socket and residual limb. However, this design does not solve the problem of taking off the prosthetic to accommodate for large volume changes, only offers some relief during activities.
Pros
-
Custom Seals for vacuum sockets
-
Flexible material adjusts for small volume changes
-
Maintains force between the socket and residual limb for small volume fluctuations.
-
Easy to use
-
Easy to put on
Cons
-
Not capable of automatically adjusting
-
Might need to be changed throughout the day
-
Not one-size fits all for activity levels. Need multiple seals for different activities
Manually Adjustable Tightening System
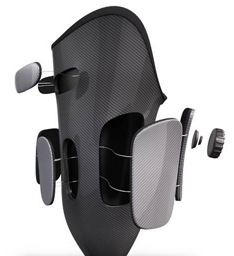
Easy to use manual tightening system. Reduces the need to change socks throughout the day. However, this design is not automatic and the user must know the appropriate time to adjust the socket.
Pros
-
Able to apply pressure to specific points
-
Easily adjustable by user
Cons
-
Not automatic adjustment
-
User might only adjust when they begin to feel pain and discomfort in socket
Flexible Subischial Vacuum Socket
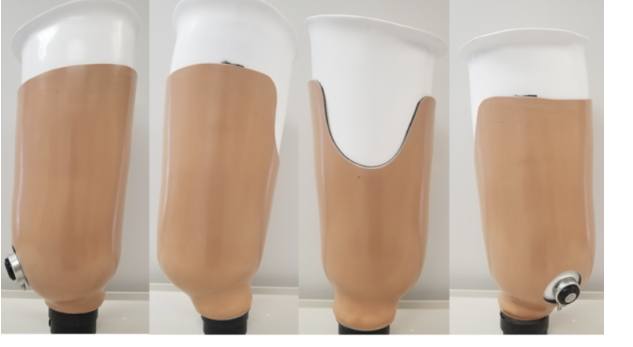
Vacuum seal stays on tight with volume fluctuations using a one-way valve, however, our client indicated they want something that could accommodate people with bad skin.
Pros
-
Silicon Liners offer comfort
-
The vacuum creates an even pressure distribution on the leg
-
The socket stays on tight
Cons
-
Vacuum sockets can cause damage to skin tissue especially in people with poor skin
Background and Problem Analysis
Volume Changes
-
Residual limb volume can fluctuate up to approximately 6% in a single day, although 3%-5% is common for most people [1].
-
From qualitative clinical observations, a “good” socket fit typically becomes an “acceptable” fit after approximately 5% volume loss or 2.5% volume gain, and becomes “unacceptable” after approximately 10% volume loss or 5% volume gain [2].
-
The ability to accurately measure and respond to these changes in volume is necessary for a successful solution. For a successful project, potential solutions must account for these volume changes throughout the day, ideally adjusting automatically
Sock Usage
-
Amputees compensate for volume change by putting on more socks throughout the day.
-
Most amputees need to add anywhere from 1 to 11 socks per day, 5 socks on average. Socks are typically added around 3 times per day to accommodate for the volume fluctuations.
-
This process of adding socks requires the user to take the prosthetic off in order to slip on the sock. The incorrect number of socks on an amputee can cause serious discomfort and even serious medical issues [3].
-
The ability to accommodate for a volume change without the use of additional socks would account for a successful design.
Stakeholder Analysis
1) Lower Leg Amputees
- Safety: Must not get caught on edges or other objects. Must have no detrimental effects on the user’s health. These people will use the device to help them reduce medical complications in their leg while using the prosthetic.
- Size/Shape: Allows for comfortable and normal activities in day to day life.
- Comfort: The amputees’ ability to walk, run, and balance could be affected by the design. The design should not inhibit the patient’s locomotion. The amputees’ level of comfort throughout the day will be directly impacted by the ergonomics of the design.
- Ease of Use: Can’t be over-complicated for use by an amputee. Easy to put on and take off throughout the day.
- Uninsured Cost: Any extra costs for maintenance could result in money out of pocket from the amputee.
- Durability: Material must not fail due to fatigue.
2) Prosthetic Clinicians
- Fitment: The design will affect the clinician’s ability to work with different kinds of people. The design must have customization for each patient.
- Training: The clinician must be have expertise about the design in order to utilize it for different patients. The clinician will also be responding first hand to patients concerns.
- Marketing: The Clinician will have first hand experience of the amputees’ success or failure with the socket and needs to know why design decisions were made or not made. The clinician will recommend our design to future amputees. They will need to know the benefits of the socket to promote it to new customers.
3) Manufacturer
- Equipment Compatibility: Molding of residual limb and unique surfaces may require new manufacturing equipment.
- Tools: Being able to design for existing methods and tools of assembly will go a long ways to reducing cost, in turn increasing accessibility.
- Tolerances: Total time to manufacture and material required will be affected by the magnitude of design tolerances.
4) Insurance Companies
- Insurance Cost: Design must be able to be covered by insurance companies.
- Validation Process: This stakeholder will determine if the design qualifies for insurance coverage. The design must offer significant benefits to the amputee’s quality of life for it to meet insurance standards.
Needs
Need | Description of Need | Justification | Required |
---|---|---|---|
1a | Material cannot cause abrasions or otherwise damage the skin of the user | Abrasions can lead to infection or other medical complication | Y |
1b | Fastening device cannot be too tight | Fastening device must not cause restriction or discomfort such that the health and/or well being of the user is compromised | Y |
1c | Device needs to minimize or eliminate the risk of electric shock | Any electronics placed in the device will need to not cause injury to the user | Y |
2a | Must be able to sense the volume change as seen by the user throughout the day. | An autonomous socket was a constraint given during the initial meeting with advisor. | Y |
2b | Able to adjust to the volume change seen by the user throughout the day | Constraint | Y |
3 | Functionality. The design must be wearable for amputees throughout the day and be capable to accommodate various lifestyles. | The design must be functional for use by customers. | Y |
4 | Comfort. The design must be comfortable for extended periods of use. | If the design is not comfortable, it will not be utilized. | Y |
5 | Easy to Use. The design must be able to be used without extensive training. | An advisor, a prosthetic clinician, stated that many amputees do not use various types of prosthetics because they are over-complicated. | Y |
6 | Compact. The design must fit the user’s limb and cannot negatively affect the user’s balance or impede movement. | If the design does not reasonably fit the user it cannot be used. | Y |
7 | Durable. Customers will be relying on this device to work at all times to support them and their range of motion. | The device will need to be able to support not only the user but the forces that are seen through a regular range of motion, actions, activities by the user. | Y |
8 | Customizable. It should be able to integrate into existing products/technologies. | Listed in Stakeholder Analysis. It would be ideal if it could accommodate 95% of patients. However, It may need to be made specific to each customer. | N |
9 | Waterproof. The design should not yield due to adverse weather. | The device should be reasonably waterproof to ensure functionality of the design and the safety of the user. | N |
10 | It can be made using existing manufacturing equipment. | The product will be more accessible to amputees if manufacturers are able to make it. | N |
11 | Comparable pricing to other options on the market. | Insurance companies could potentially cover the cost of the prosthetic socket for the amputee. The device has to be a reasonable price compared to current sockets on the market. | N |
12 | Informative and simple instructions for users and physical therapists/clinicians. | One of the stakeholders would be those responsible for training patients on how to use these prosthetics. As such they will need to be taught themselves before they can begin recommending and implementing our design. | N |
Specifications
Spec Item | Related Need | Specification | Justification and Reference | Required Y/N |
---|---|---|---|---|
A | 1 | Must conform to safety standards outlined in the Standards for Prosthetics and Orthotics. Section 2.3 Technical Standards. | World Health Organization (WHO) Prosthetic Standards and Regulations. | Y |
B | 2,3 | The operators should not have to readjust or add 1 ply (0.7mm) socks more than once per day. | This is a customer constraint as directed by our advisors. | Y |
C | 3,4,8 | Must be able to adjust for an average of a 6% change in volume of the residual limb for the prosthetic socket. | Customer request. The average volume change is 6% over the course of a day according to Montgomery, J., Vaughan et al. [4] | Y |
D | 9 | The product needs to be dustproof and waterproof within 1 meter. | Per Ingress code IP57 and customer constraint. | Y |
E | 3,4 | Must maintain a pressure of 20-60 kPa between the socket and leg varying per customer. | Minimum pressure must be maintained to provide stability. [6] | Y |
F | 11 | The prototype must be deliverable under a $500 budget. | Budget specified from Bronco MBE. | Y |
G | 4 | In comparison to existing sockets, a user must define equality or improvement for comfort (scale of 10). | The design must be considered reasonably comfortable compared to existing designs on the market. | Y |
H | 1,4 | Must be made of silicon or another material that is skin-friendly. | Must be made of material acceptable by the ASM International Handbook of Materials for Medical Devices. | Y |
I | 8 | The customer will have an opportunity to customize the aesthetics or socket shape of the final design so long as it does not compromise the integrity of the device. | The design must be accomodating for the customer to satisfy their needs depending on their lifestyles. | N |
J | 3,5 | For the final design to be considered easily operable, it should take no longer than one minute to don or doff the prosthetic. | Donning and doffing the prosthetic as a daily activity will begin to take a large amount of time over the course of a life. Making this as seamless as possible will add to customer satisfaction. | N |
K | 7 | The socket must withstand temperatures between -10 to 120°F. | The device must be able to withstand a range of temperatures throughout the year. | N |
L | 1,3,7 | Be able to support the weight of a person (up to 350 lbs). | The weight of 95% of Americans is less than 350 lbs. [8] | N |
Form and Function
Control System Design
To demonstrate the functionality of the pressure sensors and motors, we will first create a control system separate from the prosthetic. The purpose of this test is to test our control system. We will fine tune the coding to create a relationship between the applied pressure and the turning of the worm gear.
-
We will directly measure the force inside the socket exerted on the residual limb using pressure resistors.
-
An Arduino will receive the pressure input and control a worm geared motor that adjusts the tension of the tightening cable.
-
Worm gearing is important to prevent any backsliding of the motor.
-
Previous Design Iterations
Below are some drawings and iterations of our design.
Analysis of Performance
Modified Automatic Tightening System
This design makes use of existing socket tightening systems and automates the tightening process.
The design would utilize force sensing resistors located on the panel in contact with the tibia to measure the pressure on the limb. The tibia is one of three identified contact points with the existing socket. The data will be sent to an Arduino that would reside under the boa tensioner. The Arduino would interpret the data and drive a servo motor that would lead into a pulley system which drives a worm gear system to control the boa tensioner. The worm gear allows the system to be controlled in both directions to accommodate for increases or decreases in volume.
Pressure Resistor
As per the list of specification, the user sees a pressure of around 20-60kPa in order to hold the socket to their residual limb. The sensor that has been selected has bounds from 0.646-151kPa. Being well within the range that the prosthetic will see and easy to adhere to the socket itself, these resistors will be an excellent choice for data collection.
Arduino
The Arduino will be able to receive analogue input from the sensor and use it to make decisions controlling the motor.
Worm Geared Box DC Motor
The original Boa system uses a ratcheting mechanism to ensure it does not loosen during use. To achieve this same effect while also being able to tighten and loosen as necessary, a worm gear set will be used to provide one-way power transmission from the motor to the prosthetic. This will keep the load off of the motor when not actively tightening/loosening, as well as prevent “backsliding”. The motor selected provides 16kg-cm of torque while maintaining 12RPM.
Tightening System
The manual tightening system has been provided by Kormylo – Advanced Prosthetics and Orthotics. This device has mapped out areas that have been determined as areas of contact critical for maintaining a tight fit with the patient. The Boa system is integrated into a prosthetic socket and will be modified in order to accommodate for the added electronics.
Flow Chart for Proposed Control System
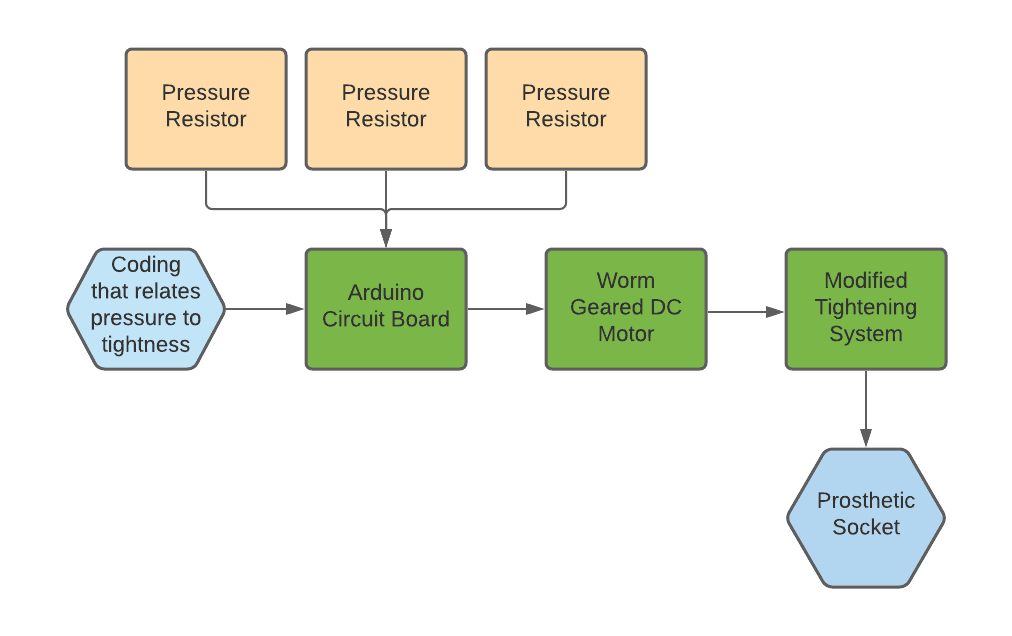
Testing of Performance
Our concept will need to be tested to ensure both safety and functionality of the socket.
Testing
-
Resistors will be aligned on inner panels of the prosthetic socket
-
Resistors will be tested in various locations inside the socket to determine the positions that yield optimal data quality.
-
Inside the prosthetic, a sphygmomanometer will be inflated to replicate the volume fluctuations seen by the user throughout the course of the day
-
The sphygmomanometer will give a pressure dial readout that can be used in data collection
-
Device will be tested until motor failure
-
Sphygmomanometer will inflate and deflate to find the upper and lower limits for the device
Bill of Materials
Access Required
Development Schedule
-
-
Meeting to Discuss Concept Proposal
-
Make necessary changes to Narrative
-
Publish Narrative website
-
Summer
-
-
Break from Design Project
-
September
-
-
Reboot Team
-
Identify size of prosthetic that we are modeling our design to.
-
POA Managerial Meeting
-
Group meeting to identify key design locations.
-
Calculate gear ratio and motor size
-
Draw SOLIDWORKS 3D model and 2D drawings.
-
Concept Design Finalization
-
Make Bill of Materials
-
CDR with Clients
-
Purchase items from Bill of Materials
-
Identify key testing elements
-
October
-
-
Model and Build Prototype
-
Build physical model from the SOLIDWORKS assembly.
-
Build testing apparatus (ballistic gel, pig leg, etc.)
-
Testing to ensure functionality of product.
-
Safety testing to ensure that the product is not harmful to the user.
-
Analyze results from testing
-
November
-
-
Compile test results
-
Modify prototype
-
Show how test results conform to our specifications
-
December
-
-
Finalize product for showcase
-
Prepare for online showcase
-
Present finalized design
-
Senior design showcase
-
References
- Sanders, J. E., Harrison, D. S., Allyn, K. J., & Myers, T. R. (2009, December). Clinical utility of in-socket residual limb volume change measurement: case study results. Retrieved from https://www.ncbi.nlm.nih.gov/pmc/articles/PMC4435543/
- Sanders, J. E., & Fatone, S. (2011). Residual limb volume change: systematic review of measurement and management. Journal of rehabilitation research and development, 48(8), 949–986. Retrieved from https://doi.org/10.1682/jrrd.2010.09.0189
- Bloomer, Gary. Prosthetic Sock Management Tool. TechLink, Retrieved from https://techlinkcenter.org/technologies/prosthetic-sock-management-tool/
- Montgomery, J., Vaughan, M., and Crawford, R. (July 9, 2009). “Design of an Actuated Volume Compensating SLS Prosthetic Socket.” J. Med. Devices. June 2009; 3(2): 027534.
- Chris. (2019, December 19). Average Vertical Jump: By Age, Sport, NBA and NFL. Retrieved from http://www.homeexerciseequipmenthq.com/average-vertical-jump/
- Steer, J.W., Worsley, P.R., Browne, M. et al. Predictive prosthetic socket design: part 1—population-based evaluation of transtibial prosthetic sockets by FEA-driven surrogate modelling. Biomech Model Mechanobiol (2019). Retrieved from https://doi.org/10.1007/s10237-019-01195-5
- APRadmin. (2014, May 20). What is the “True” Weight of Amputees? Retrieved from https://aprpros.com/true-weight-amputees/
- Centers for Disease Control and Prevention. (2017, May 3). FastStats – Body Measurements. Retrieved from https://www.cdc.gov/nchs/fastats/body-measurements.htm