For 42 years, a small group of health and safety experts has been a part of Boise State while supporting hundreds of Idaho’s small businesses and their employees with free training, lifesaving education, and onsite assessment visits.
The Idaho Occupational Safety and Health Consultation Program, known informally as OSHCon and currently housed at the Yanke Family Research Park, hit the 42-year mark in October. The federally mandated program is a powerful, if little-known, resource for businesses with fewer than 500 employees.
The OSHCon team is primarily engaged in high-hazard settings — think construction, sawmills, grain silos and metal foundries, for example, or aircraft, manufacturing and industrial agriculture. Program Manager Kimberli Reynolds and her team of three consultants conduct onsite consultation visits across this great state each year to advise, educate, and make recommendations to employers regarding compliance with occupational safety and health regulations administered by OSHA.
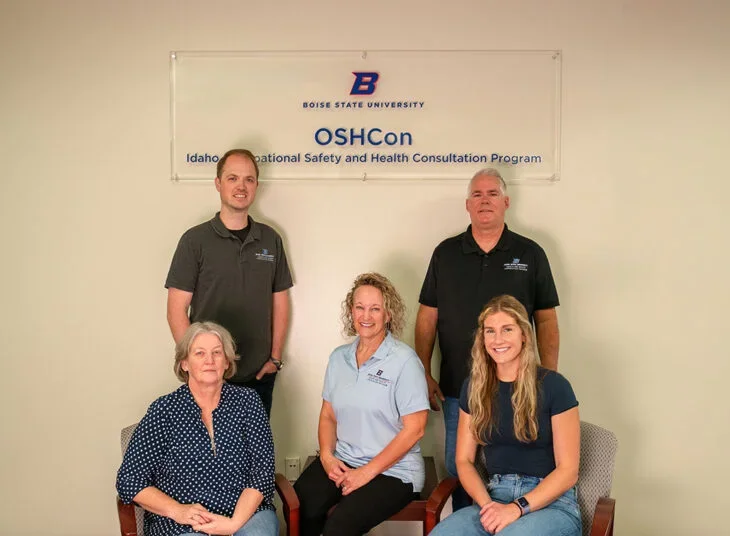
They are not OSHA. The Occupational Safety and Health Administration (OSHA), established in 1970, conducts inspections and can levy penalties.
OSHCon was created as a resource following OSHA’s establishment in 1970. The program is not involved in enforcement activities, rather it seeks to help employers understand the regulations and how to apply them. OSHCon is federally funded and receives in-kind support from Boise State, and the College of Health Sciences. Services are private, confidential, and free.
The program’s highly trained consultants conduct onsite consultations with companies that request its services. Consultants can perform safety evaluations and health evaluations referred to as industrial hygiene. Consultants work to make recommendations related to workplace hazards, or to assess noise and air quality; all with the goal of safer and healthier workplaces.
Recognizing companies dedication to healthy and safe workplaces
Some companies have been working with the program for years; others call occasionally. A handful of companies have achieved the Safety & Health Achievement Recognition Program (SHARP) status for continuous, outstanding safety and health performance. As Reynolds points out, that SHARP distinction can be a selling point for a business’s customers, and OSHA looks favorably on these companies’ proactive stance.
From Aircraft…
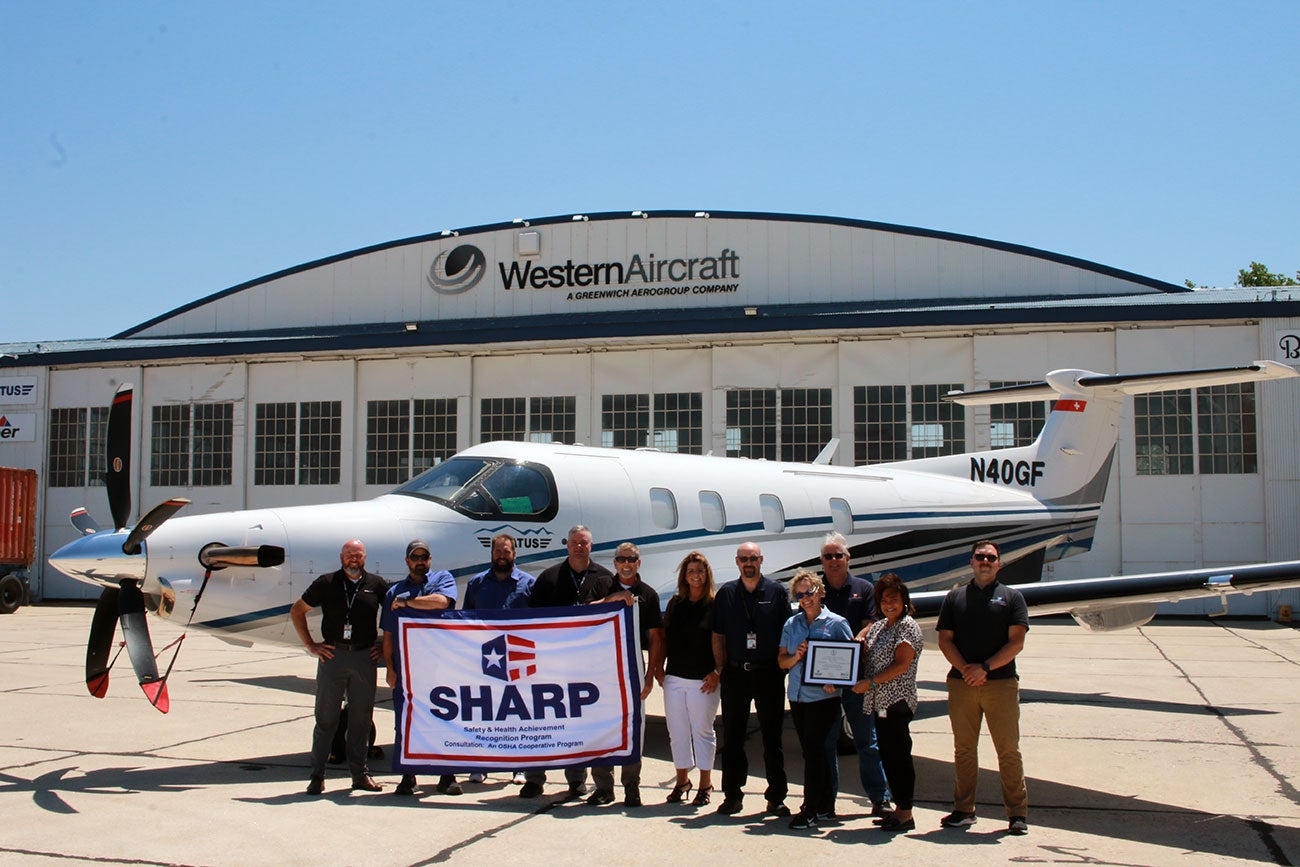
Western Aircraft is one of those long-time SHARP awardees. The company of several hundred employees located near the Boise airport maintains, inspects and modifies private and corporate aircraft.
“We get to celebrate with this company a great deal,” Reynolds said. “They achieved SHARP designation in 2006 and have led with exemplary safety.”
Jeff Wallin is the company’s production scheduler/environmental health and safety manager. The program, he said, has been very beneficial from a variety of standpoints.
“As I came into this position, it gave me an outline on what our mandatory responsibilities are,” he said. “They’ve been a great help to us. Tips, pointers … an extra set of eyes that shows and tells and explains.
“Just by knowing that they’re on our side, and it helps our overall safety program. It helps us integrate employees to actively participate in our program. They help do that, just by their presence.”
To bronze manufacturing…
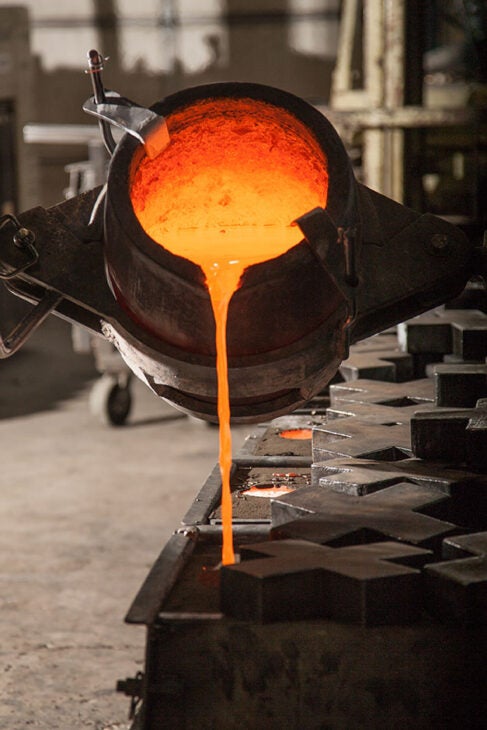
Billy Collins is the senior manager of production and safety for Sun Valley Bronze, which handcrafts hardware, sinks, bath accessories and a variety of other fixtures for resorts and large residential properties.
With about 60 employees, the company has offices and manufacturing space in Bellevue and a metal foundry in Carey. They’ve been collaborating with OSHCon for more than two decades to ensure they are creating and maintaining a safe workplace. Sun Valley Bronze is one of the companies that also utilizes OSHCon’s free industrial hygiene services regularly for breathing air hazards such as metal fumes.
“They are awesome,” Collins said of the program. “It’s something that is totally necessary, that all small business should use. It’s a really nice asset.”
The partnership has helped to support the company’s safety environment, he said, noting that at one point, an employee came up with a safety design as the result of an OSHCon visit that was put into place.
“It kind of creates a culture, because employees see you with them,” Collins said. “With them being in there and making things safer, the employees partake in that. The input resonates, and the culture becomes safer. They’re there to help.”
To construction…
In North Idaho, general contractor Ginno Construction’s safety and environmental officer, Greg Rodriguez, routinely has invited program consultants to join him at active construction sites, usually commercial but also high-end residential projects. With 10 to 15 workers moving about a job site, Rodriguez is mindful of the risk of everything from falls from ladders and roofs to electrocution and cave-ins. The team has provided valuable perspective at a variety of points in the company’s work.
“I’ve worked with them for quite a while,” Rodriguez said. “I don’t know it all and I don’t see it all. They help me see what I may be missing, and they back me up on what I’m trying to educate workers on regarding their safety.”
“To be able to walk through and say, ‘What do you think of this?’ It’s good to look at issues, and they’re always very positive and great to work with. That’s one of the reasons that I bring them on. They’re very helpful.”
Education means prevention for the future
From doctors’ and veterinarians’ offices to sawmills and construction sites, the consultants are trained to offer ideas and suggestions. With Reynolds and the team, it’s about everyone’s safety and health, minimizing downtime, and optimizing productivity and morale, for workers and management alike.
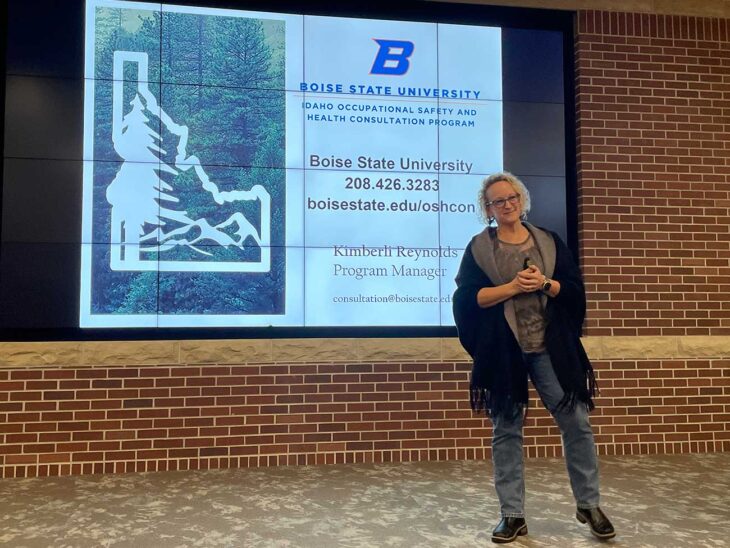
It’s also about education — lots and lots of education.
“Most companies want to do it right,” Reynolds said. “Safety and health is never going away. You can correct the hazard while you’re standing there, and the hazard can reintroduce itself.
“We can walk through and show the employer what the hazards are and give pointers on how to mitigate those hazards.”
“OSCHon is a small and mighty team”, says Reynolds. They are always on the move, so OSHCon is looking at ways to expand its reach. A current pilot project aims to bring digital and virtual reality safety training — again, free of charge — to small businesses in Idaho. The program currently has hundreds of DVDs available through its lending library, but sees the need to evolve its technology to keep up with the needs of employers. Reynolds is also evaluating potential industrial hygiene internships for Boise State and the College of Health Sciences in the future.
The need for OSHCon’s services seems only to be trending upward, and not only in Idaho. Multiple changes in the workforce — a desire by many to work from home post-COVID, persistent staffing and retention challenges and turnover in many industries – have resulted in, among other things, higher on-the-job injury and fatality rates across the nation. Many of these are in industries the OSHCon team prioritizes for service.
Because many of the businesses and companies that OSHCon works with are too small to have their own safety officers, Reynolds and the team become the de facto line of defense.
“We come in and we’re kind of that safety person for them,” Reynolds said. “And they can have us in every year, just to help out with that. They can also call us anytime to answer questions.”